Partial Discharge Management 101: Prevention & Causes
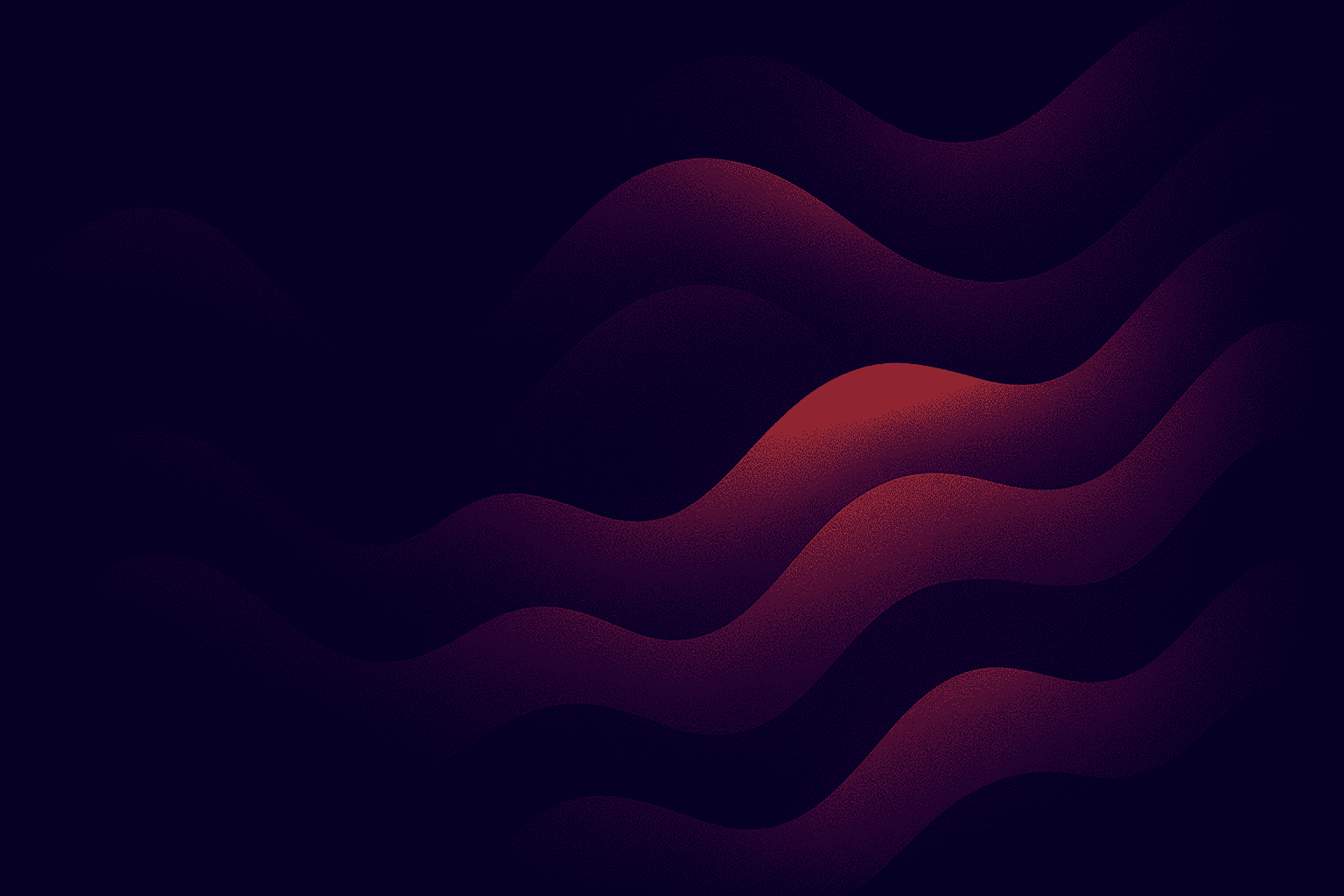
Partial discharge (PD) is a localised electrical discharge that only partially bridges the insulation between conductors, and preventing it is crucial for the reliability and longevity of electrical equipment.
PDs can degrade insulation, which may lead to equipment failure and costly repairs. Effective prevention involves strategies focusing on design, manufacturing, operation, and maintenance.
What is Partial Discharge Prevention?
PD prevention is crucial for maintaining the reliability and longevity of high-voltage systems, and it involves strategies that address design, manufacturing, operation, and maintenance. PDs are localised electrical discharges that can lead to insulation degradation and equipment failure.
How Does it Work?
PD prevention is a multifaceted approach that aims to ensure the reliability and longevity of high-voltage systems by addressing potential issues during manufacturing, operation and maintenance.
Manufacturing Processes
Manufacturing processes play a critical role in PD prevention. Its likelihood of PD can be significantly reduced, ensuring more reliable and longer-lasting equipment.
Dust controlÂ
Maintaining a clean environment during manufacturing is vital, as dust and foreign matter are significant contributors to PD. Metallic particles as small as 1.5ÎĽm can cause discharges under an electric field.Â
Manufacturers must maintain clean environments with dust-proof workshops and strict control over dust exposure.
Centralised Processing of Insulating Parts
Insulating components should be processed in isolated areas, separate from other dust-producing zones. This prevents contamination, especially from metal dust, which is difficult to remove once it adheres to the parts
Silicon Steel Plate Burrs
The burrs on silicon steel plates used in transformer cores should be minimised because they can cause short circuits, increase losses and lead to discharges. The burrs can detach and cause discharges elsewhere. The burrs of 110KV products should not be greater than 0.03mm.
Leads and Cold-Pressed Terminals
Using cold-pressed terminals avoids the spatter slag that comes with phosphor copper welding, which can diffuse to the body and insulator. Source boundary areas must be separated by submerged asbestos wires, and any moisture must be removed after insulating the winding to avoid increased partial discharge.
Rounded Component Edges
Rounding the edges of metal components, such as clamps, pull plates, pads, brackets, pressure plates, and outlet edges, can improve field power distribution and increase the discharge starting voltage. It also helps prevent friction from generating iron filings. All contact points, such as clip hanging holes, should be rounded.
After vacuum drying, the equipment should be cleaned in dust-proof areas, especially if exposed to air for more than 8 hours. The body must be dried again prior to vacuuming and tank filling. Dehumidification of stems is also critical because stem insulation absorbs moisture during the trimming phase.
Operational Practices
Vacuum lubrication involves injecting transformer oil under vacuum to eliminate air pockets in the insulation structure. This ensures the oil is completely absorbed into the transformer body, increasing the penetration of the insulation material which reduces the likelihood of discharges. Wait at least 72 hours after injection to allow for sufficient absorption time.
Proper sealing of the fuel tank and other parts is essential to prevent moisture ingress, as moisture absorption can cause transformer oil and insulation to degrade, creating conditions that favor PD.
Monitoring and Maintenance
Effective monitoring and maintenance are crucial for PD discharge-related failures in high-voltage systems. Regular monitoring helps identify PD early, allowing for timely maintenance and repairs.
Regular Inspections
Using methods like this by ultrasonic scanning, thermography and electrical measurements, can detect and address potential issues early.
Ultrasonic ScanningÂ
It is useful for detecting surface and corona PD. A handheld probe microphone can be used for field operations, which allows for frequent assessments at lower costs.
It needs a structured approach using simulations and quantitative measurements such as the average absolute of acoustic pressure signals (pavg) enhances the process. A threshold of 0.5 ÎĽV for pavg can help prevent misinterpretation by field inspectors.
ThermographyÂ
It uses infrared imaging to measure temperature and can detect heat anomalies that may indicate issues such as electrical overloads or insulation failures.
When capturing thermal images, make sure the target system is operating at a minimum 40% load. Get close to the target and do not measure through doors or glass, and account for wind and ambient air temperatures.
Partial Discharge Scanning
It detects electrical discharges in high-voltage equipment, using an unsupervised, three-phase method for greater accuracy without prior training, ideal for real-time measurement.
Data Analysis
Accumulate both numeric temperatures and thermal images to facilitate long-term data analysis, as temperature trends will show you where to investigate more and where inspections can be less frequent.Â
Create a baseline image database, assign alarm temperatures, and upload the latest version to your camera before inspections. An alarm signals a significant temperature change requiring attention.
Predictive Maintenance ProgramsÂ
It can reduce maintenance costs and equipment repair costs, and a properly functioning program can provide savings of 30-40% over reactive maintenance. Industrial predictive maintenance programs can result in a return on investment of 10 times and eliminate breakdowns by 70-75%.
Key factors for effective PD prevention
Effective PD prevention relies on a combination of factors, from manufacturing processes to ongoing maintenance and monitoring. By addressing these key factors, the risk of partial discharge can be significantly reduced, thereby enhancing the reliability, safety, and longevity of high-voltage systems.
Understanding PD
It's essential to know the causes and types of PD, which include corona, surface and internal discharges. Identifying the specific type of discharge can help determine the best course of action.
Corona DischargesÂ
occur near metallic extremities due to non-uniform electric field distribution, and weather conditions can cause them to manifest as a glow near electrodes.
Internal DischargesÂ
It occurs in cavities within solid or liquid dielectrics, leading to deterioration of the equipment’s insulation.
Surface DischargesÂ
It occurs during voltage surges at the boundaries between conductors and insulators. They are also common in areas characterised by interfaces among metals, solid insulators, and gases.
Material selection
PD prevention is crucial in high-voltage systems to ensure their longevity and reliability. Several factors can contribute to PD, including installation defects, design flaws, manufacturing voids, particle contamination, adverse environments and aging.Â
Choose insulating materials with high dielectric strength and thermal conductivity to prevent partial discharge. The quality of insulating materials and their correct application are key to preventing discharges.
Managing PD effectively involves careful material selection and design considerations to minimise the likelihood of these issues.
Safety
Adhere to safety standards such as National Fire Protection Association (NFPA) 70E and Occupational Safety and Health Administration (OSHA) standards when performing inspections or maintenance.
By implementing these measures, the occurrence of partial discharges can be reduced, ensuring the reliability of electrical systems and minimizing the risk of equipment failure.
To Conclude
Partial Discharge (PD) is a major issue in high-voltage systems, but it can be managed with proper prevention and regular monitoring. A comprehensive approach is key to minimising risks.
Inframatrix supports PD prevention with advanced FLIR thermal cameras, helping detect electrical faults early to improve reliability, prevent failures, and ensure safe operations.